2021-12-02 | Tech
Microsoft Word. Adobe Photoshop. Whatsapp. Some software is so ubiquitous that you don’t even think that an alternative might be a good idea, or even exist. But often they do exist, and you should consider switching.
Why do I think you should switch? The two biggest reasons, are Google and Adobe. Adobe removed the ability to purchase software outright, forcing users into a monthly subscription. Google are just…well…Google. They sell your soul to the highest bidder.
I stopped using Google Analytics a few months ago on here, opting instead for a locally hosted Matomo analytics plugin, which does everything I want it to (and more). What it doesn’t do, which is the real drawcard, is send the analytics on to anyone else. The analytics are for me, and for me only.
I subscribe to a daily email called The Sizzle (https://thesizzle.com.au/), and today it alerted me to the website called Switching Software (https://swiso.org/). It’s super simple: look for the program you use, click on it, and it will tell you what the open source/free/non-evil/ethical alternatives that are available.
I’ve written about Signal before here: Why do I use Signal?, and it is one of the alternatives to WhatsApp – the one that I recommend. It has an edge over WhatsApp in that it will take over (if you want it to) as the default SMS app and allow you to keep SMS and Signal messages in the same encrypted database on your phone.
Switching Software mentions Matomo as the replacement for Google Analytics, along with another few options – a switch I already made.
I dumped Adobe for the Affinity software suite – which isn’t free, but all three applications cost $150 all up when they were on special, for a permanent licence.
I use OwnCloud instead of Dropbox. This is a faff, and not for everyone, because you have to host your own server. But if you have access to a machine that’s always online, it’s a good option.
I host my own mail server using Mail In A Box (https://mailinabox.email/) rather than relying on Gmail. Also a faff, because spam restrictions are so tight these days that if you aren’t one of the big players (Microsoft/Google) you’re very much a second class netizen. With patience and some polite emails to whatever spam filter is blocking you and it’s possible to get unblocked and then it works a treat.
It’s worth while investigating these. I’ve just downloaded kdenlive, a non-linear video editing application to replace Adobe Premiere Pro. I’ll see how it is and maybe post a review down the track.
2021-11-10 | Tech
If I run this domain through Qualsys’s SSL Server test, I get an A+. Which feels like a good score. I followed someone else’s instructions on how to do this, but I can’t remember where that was, so I figure putting the configuration here will be handy for me and, potentially, you.
SSLEngine on
SSLProtocol all -SSLv2 -SSLv3 -TLSv1 -TLSv1.1
SSLCipherSuite HIGH:!aNULL:!MD5:!3DES
SSLHonorCipherOrder on
SSLCompression off
SSLOptions +StrictRequire
Header always set Strict-Transport-Security "max-age=15552000; includeSubDomains; preload"
2021-11-10 | Tech
Background
I had a reason to see if I could get Ghost running alongside this WordPress install today, and it turns out that once you follow the correct and up-to-date instructions, it’s quite simple. I run Apache rather than nginx, so the default instructions don’t work. The magic happens with the RequestHeader line and the whole https component of the VirtualHost looks like this:
<VirtualHost *:443>
ServerAdmin webmaster@localhost
ServerName ghostblog.domain
ErrorLog ${APACHE_LOG_DIR}/error.log
CustomLog ${APACHE_LOG_DIR}/access.log combined
ProxyPass / http://127.0.0.1:2368/
ProxyPassReverse / http://127.0.0.1:2368/
ProxyPreserveHost On
RequestHeader Set X-Forwarded-Proto "https"
Include /etc/letsencrypt/options-ssl-apache.conf
SSLCertificateFile /etc/letsencrypt/live/ghostblog.domain/fullchain.pem
SSLCertificateKeyFile /etc/letsencrypt/live/ghostblog.domain/privkey.pem
</VirtualHost>
There’s also the redirect from http to https but I do that in a separate VirtualHost with a permanent redirect. Without the RequestHeader line, you end up with a lot of internal redirects when you try to access the site over https.
Following the official installation works well, and if it detects that nginx isn’t installed, Ghost-CLI will let you skip that part of the configuation and it trusts that you’ll figure it out some other way.
Ghost-CLI also performs the database configuration and stuff for you, assuming you know the/a MySQL username and password on your server.
Thoughts
I only had a cursory look inside Ghost and my first thought is that it’s so quick. Really, really quick. I’m tempted to move this site there. Or maybe I’ll make bitterswede.com a thing in Ghost and slowly migrate across. The main thing that’s getting in the way of moving over is that I’ve used a theme called Divi which I suspect has inserted a lot of garbage into posts made with the Divi Builder.
One day, maybe.
.
.
.
2021-07-04 | Food
Throw everything into a blender: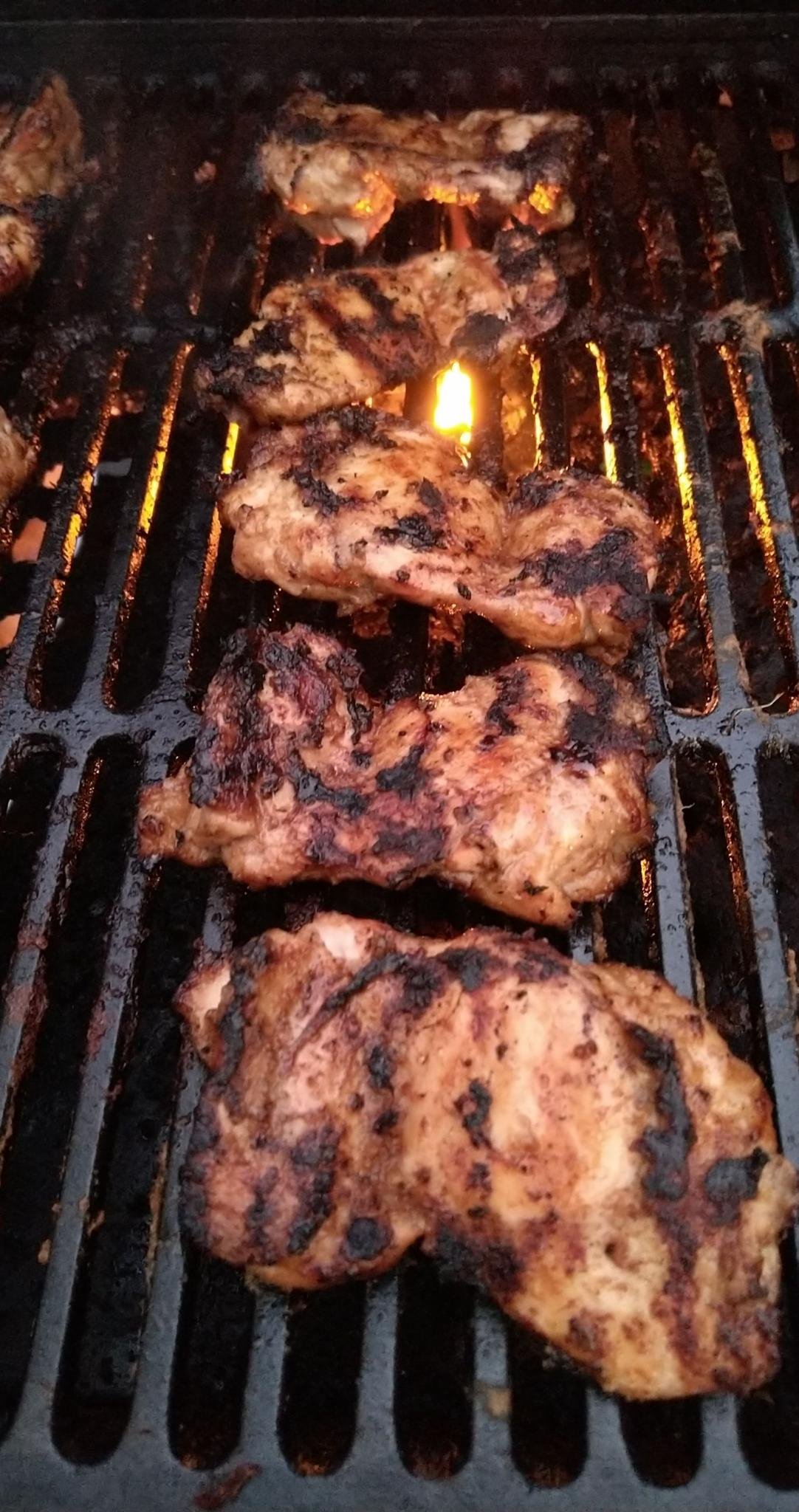
Half a peeled brown onion
A 2.5 x 2.5 x 2.5 (ish!) cm cube of peeled ginger
2 cloves of garlic
2 tsp of sugar (probably optional)
2-3 tbsp of fish sauce and soy sauce
1 tbsp of chinese five-spice mix
1 birds eye chilli or similar
Some oil, and a cup or so of water
I also put some Kecap Manis in, but that’s probably not right. Not that this is authentic anyway.
Blend everything.
Marinate a kilo (or so) of chicken thighs for as long as you can. About an hour is enough, but longer will probably be better.
Cook on the open flame part of the BBQ until cooked (75°C is the safe temperature for chicken, apparently).
.
.
.
.
2021-02-22 | Tech
“Are you home Thursday night, or do you have yoga?”
“Are the kids going anywhere this weekend?”
“I’m sure I mentioned that!”
I’ve wanted to build a family week planner for ages that puts everyone’s week on a easy to read screen somewhere in the house. Maybe somewhat surprisingly, I’m not a big fan of home automation or a “smart” house, so I don’t want this thing to alert me in the morning that “Today J has five appointments blah blah”. I just want to be able to look at it every now and again and see what’s coming up.
I used to run an Exchange server for all my various email accounts, and that was good, but it started becoming an issue with out-of-date software. The option to move to O365 was there, but it feels expensive, especially since several of the accounts are for the kids and aren’t “serious” mailboxen.
I spun up a cheap (US$10/month) Ubuntu server on Linode and ran the setup script for Mail-in-a-Box, which has worked (touch wood) nearly perfectly since. The issues so far have been pretty minimal. Microsoft was blocking my IP address for all Outlook-themed email services (live.com, hotmail.com, etc), but emailing them asking them to stop worked. When I reboot the server, the Outlook app on an iPhone stops syncing, and the account has to be removed and re-added. I also need to figure out how to make it send calendar invites properly over email.
Considering I have about 10 mailboxen on there, I’m way ahead in terms of cost.
The Mail-in-a-Box script installs NextCloud (an OwnCloud fork), which has a WebDAV implementation for calendar and contacts.
Step 1 for getting a week planner up will be to figure out how to interrogate the CalDAV server with some sort of programming language. I’m comfortable with PHP, so that’s what I’m going to do it with. Specifically, using cURL from PHP and then stuffing the results into an array to display later.
A bit of reading and digging in the WebDAV standards has lead me to being able to grab calendar entries for an account on the serer with the following command:
curl --request REPORT --header "Depth: 1" --header "Content-Type: text/xml" --data "<c:calendar-query xmlns:d='DAV:' xmlns:c='urn:ietf:params:xml:ns:caldav'><d:prop><d:getetag /><c:calendar-data /></d:prop><c:filter><c:comp-filter name='VCALENDAR'><c:comp-filter name='VEVENT'><c:time-range start='20210218T000000' end='20210225T000000'/></c:comp-filter></c:comp-filter></c:filter></c:calendar-query>" --user nextclouduser:nextcloudpass https://box.example.com/cloud/remote.php/dav/calendars/nextclouduser/personal/
The time-range field will limit the calendar entries that will be grabbed based on the starting-time.
This spits forth a large blob of data that will be interrogated later.
There will be tricky things to over-come like multi-day events and the like, but based on some work I’ve done previously with a calendar and loading events, I think I have a plan.
That’s step 1 done.
Step 2 to come.